In a world where speed-to-market can make or break a product, traditional prototyping methods are often too slow, expensive, or rigid for fast-moving development cycles. Enter 3D printing — not as a gimmick, but as a transformative tool for small-batch and rapid hardware prototyping.
At Root Labs, we’ve embraced additive manufacturing as a core part of our workflow — enabling faster iteration, lower costs, and tighter control over design changes. In this post, we’ll explore how modern 3D printing is empowering small teams and independent creators to innovate like never before.
From Concept to Object in a Day
The days of waiting weeks for CNC parts or injection-molded test units are over. With an in-house FDM or resin printer, a CAD file can become a physical object in under 24 hours — sometimes within just a few hours.
We’ve used this workflow to:
- Build custom sensor enclosures for IoT projects
- Prototype ergonomic housings for handheld electronics
- Test mechanical tolerances on parts before full-scale production
With slicers like PrusaSlicer, Bambu Studio, or Cura, you can optimize prints for speed, quality, or strength — and iterate daily with minimal overhead.
Choosing the Right Technology
Not all 3D printing methods are created equal. Here’s a quick breakdown of the two most common types we use at Root Labs:
Method | Strengths | Best For |
---|---|---|
FDM (Fused Deposition Modeling) | Fast, cheap, strong | Prototypes, brackets, functional parts |
SLA (Stereolithography) | High detail, smooth finish | Precision components, product enclosures |
We frequently print in PETG or ABS for durable components, while resin is ideal for fine detail work. For strength-critical applications, carbon fiber-infused filament offers excellent rigidity without needing metal.
Real-World Applications
🔧 Rapid Electronics Prototyping
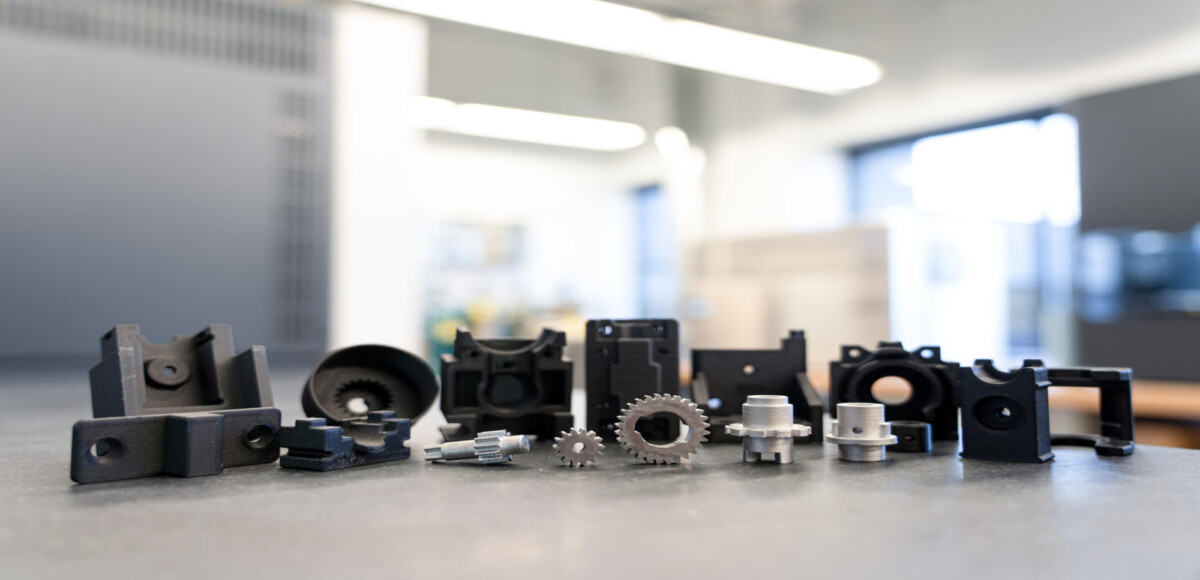
Source: Markforged
Design a board, print a housing, and have a field-ready enclosure by the end of the week. This shortens the iteration cycle dramatically — especially when paired with modular electronics platforms like Raspberry Pi or ESP32.
🏭 Low-Volume Manufacturing
Need 10–50 units of a custom part? Instead of paying for tooling or overseas delays, you can print them in-house or through a service like JLC3DP or Xometry.
💡 Proof-of-Concept Demonstrations
Clients love to see something they can touch. A 3D-printed prototype, even if not final, brings ideas to life and makes pitch meetings more compelling.
Tips for Getting the Most Out of 3D Printing
- Design for printability: Avoid overhangs, support-heavy structures, or parts that are too thin.
- Test in real-world conditions: Even great prints can fail under UV, moisture, or heat.
- Don’t fear failure: A failed print today often means a stronger part tomorrow. Every iteration is data.
The Future Is Desktop
The 3D printing revolution isn’t coming — it’s here. Affordable machines like the Bambu Labs X1 Carbon or Prusa MK4 are putting industrial-grade capability on your desk.
At Root Labs, we’ve used 3D printing to bridge the gap between ideation and execution — reducing costs, shortening timelines, and giving our clients a real competitive edge. Whether you’re building your first prototype or fine-tuning your fifth revision, 3D printing gives you the agility and control that modern product development demands.
Need help prototyping your next big idea?
Contact Root Labs — let’s bring it to life.
Leave a Reply